Understanding the many types of cold storage and controlled environments – food and beverage processing; food distribution; and public refrigerated warehousing – along with a plethora of product-specific terminologies, is the first step in diving into the world of its development. But there is much more to explore to understand the nuances of this sector.
Five cold storage specialists led a conversation at NAIOP’s I.CON Cold Storage conference this week in Atlanta to share key considerations of this hot topic. Led by Kate Lyle, NCARB, Director, Industrial Cold & Food with Ware Malcomb, the panel included Josh Cronan, vice president, ARCO Design/Build; Vince Free, president and CEO, FREEZ Construction, LLC; Todd Jessup, president of Flexspace and co-founder of FlexCold; and Dean Soll, partner, Open Concepts.
Whether a cold storage project is new build or retrofit, it’s critical to sit down with the end user to determine their needs early in the process. The requirements that will emerge from that conversation are critical to the success of the project. Questions about temperature needs, refrigeration systems, structural design, fire protection and more will set the stage for the project and its timeline.
Cold storage can take two different approaches: a greenfield project or a retrofit. Greenfield projects typically have fewer constraints, but planning and permitting timelines are longer, pushing delivery to 12-16 months. Retrofits can be quicker, around 3-12 months for delivery, but come with limited building specs and facilities that might not meet structural or utility requirements.
The biggest variables that impact cost, budget and price of a project are operational uses and what the end user needs. Refrigeration requirements, loads and rack configurations all impact costs. One of the biggest questions is time – the faster a building is needed, the more expensive it’s going to be to develop.
Each facility is going to look different, in terms of furniture, fixtures and equipment (FFE) and who sources them, as well as how a position is situated or staffed. “If a project is an extension of a production facility, there may be need for blast freezing or packing,” said Jessup. “What’s on the pallets and if it’s being handled by full pallet or by piece makes a difference in the number of workers needed in a facility, and projects at ports will require space for imports and exports, plus staging and inspecting for regulatory requirements,” he said. “FFE is a dynamic piece for developers and investors to understand, and it’s difficult to get financing in place without it.”
Comparing design-build versus design-bid-build, design-build has a distinct advantage with speed to market and costs, as the owner/developer can identify the end user’s pain points and priorities moving into the project.
Supply chain issues or items like steel, foam, switch gears and other electrical components that were especially problematic during the COVID-19 pandemic have lessened, the speakers agreed. During the peak, switch gears were taking 52 weeks for delivery, and refrigeration equipment was around 30 weeks.
Jessup said that the issue today is what he called “a people problem” and the lack of knowledgeable project managers and supervisors in this specialized space.
“The paradigm has shifted. This sector’s buildings have aged and those who have been managing them are aging out, but without an influx of young talent coming in with expertise on details like thermal envelopes, refrigeration and energy costs,” he said, noting the need for mentorship to pass down knowledge.
This filters down to subcontractors too and evaluating their staffing. Field labor is difficult to find as well, which can impinge on execution and timely delivery. “Find out the subcontractor’s capacity and their ability to add crews if needed,” said Free. “General contractors should partner with specialty contractors ahead of time and lock in those unique to a building, like electricians, refrigeration contractors.”
When it comes to structural design, Cronan said facilities keep getting taller. “The standard now is a 55’ maximum deck, and the limiting factors are equipment and fire protection. The minute those systems are approved for 60-65′, it’s all anyone will want,” he said. “Another factor is that many of these facilities are located in coastal communities, which can present challenges with weather.”
Working with insulated concrete panels (Thermomass) rather than insulated metal panels (IMP) largely depends on if the municipality will allow for IMPs that are traditionally considered less visually attractive. Thermomass provides tilt panels that hold layers of poured concrete around structural pins and insulation, resulting in a piece that can be up to 19” thick with potential issues around the joints and tie-ins with rooflines. “It takes an immense amount of coordination between design thermal subcontractors, roofing subcontractors, and the concrete subcontractors to make sure lapping, folding and sealing are all done in the proper order,” said Cronan.
“There’s no one-size-fits-all solution for cold storage out there,” said Jessup. “It starts with looking at business opportunities within the market and determining factors including the number of convertible spaces and the number of dock spaces.” Dean said he recommends skidding refrigeration packages that can be relocated or sold at the end of a lease.
Flexibility and staying nimble is key, they agreed, so that a space doesn’t become bespoke to a specific client that may not be a long-term lease.
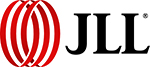
This post is brought to you by JLL, the social media and conference blog sponsor of NAIOP’s I.CON Cold Storage 2023. Learn more about JLL at www.us.jll.com or www.jll.ca.