The years leading up to the pandemic were hot for cold storage. It only promises to grow going forward.
With the cold storage vacancy rate around 4%, over 100 million square feet of cold storage space will be built in the U.S. in the next five years. As 78% of cold storage facilities in the U.S. are over 20 years old, the market promises to remain active for the foreseeable future.
The recent NAIOP publication, “Best Practices in Cold Storage Facility Development,” authored by industry experts from Ware Malcomb, FCL Builders and Cold Summit Development, explored the fundamentals of the sector. In the discussion below, three of the authors – principal Cameron M. Trefry, RA, LEED AP, and architect Kate Lyle, director, industrial cold & food, with Ware Malcomb, and Jason Fincher, vice president of strategy and logistics with Cold Summit Development – offer greater depth into the cold storage sector.
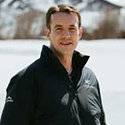
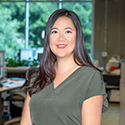
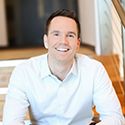
Not all markets are necessarily the same in the cold storage equation. Are any geographies or regions seeing more or less activity than others?
Trefry and Lyle: Population centers are certainly the strongest areas for cold manufacturing and distribution, which makes sense – food follows people. Areas with proximity to less developed ports – both air and sea – are also receiving increasing investments in cold storage due to the shipping shifts that are occurring. We’re also starting to see that trickle back to agriculture adjacent areas. There are certainly a lot of land-starved markets, especially near those large population centers where demand is highest. Finding locations can be challenging. In these places we can get a bit creative on how to fit our cold storage footprint. Verticality certainly helps for cold storage, and 50-foot-plus clear heights are common. We also still do a fair number of conversions, taking existing traditional warehouses and fitting in cold storage. Adding a cold storage expansion to existing facilities, whether traditional warehouse or cold storage, is also a possibility.
How has technology helped advance the cold storage model?
Trefry and Lyle: Cold technology has come a long way in recent years, and buildings are more efficiently designed than ever. Additional clear height allows for better efficiency for a wide variety of new refrigeration technologies (low charge ammonia and CO2 systems being particularly popular). Envelope elements like improved doors and dock equipment, and glycol subslab heating, avoid problems caused by ice and condensation in older facilities. Cold has also been some of the earliest adopters of automation technologies like automated storage and retrieval systems (ASRS). We also closely watch technologies related to food safety on the processing side, as well as worker safety equipment breakthroughs. The high energy loads of refrigeration made sustainable energy models challenging in the past, but microgrid technologies are allowing more and more solar power and other technologies to be utilized.
What key questions should a cold-storage customer/tenant ask when looking for or building a facility?
Fincher: This is very project specific and could include any of a hundred factors. The biggest mistake is underestimating the complexity of these projects and trying to learn as you go. Some recent examples we have seen occur in the industry are an inability to attain the necessary height variance during the zoning and entitlements phase, effectively killing the project, and one case of insufficient quality-control in a slab that resulted in an ASRS system not functioning properly and a reported $38 million in rework. Cold storage is a very complex building type and details have enormous impact.
Trefry and Lyle: Depending on what a cold building user is considering, existing building or build to suit new construction, there are a few questions they should consider.
For existing buildings, it is all about the condition of the building and expansion capability: Have there been any issues with the floor slabs or under-slab heating systems? How is the existing refrigeration system performing, what is its age of the equipment and what do maintenance records show? Is the building fully convertible to various temperature zones? Is there any possibility for expansion of the existing building on-site to accommodate future growth?
For build-to-suit new construction flexibility and expansion capability are critical as well as long term value of the asset: Is the building going to have value for the next owner? Is there any expansion capability for future growth on site? How much flexibility do you need to design/build into the project day one vs. defer to a later date?
What excites you most about the sector’s future? What gives you cause for pause in the coming five years?
Fincher: The huge scale of modern cold storage facilities, and the rate that we are building them, has the potential for significant positive impact on the environment and food accessibility, so long as the sector takes corporate responsibility seriously. We are seeing new buildings today that are 30% more energy efficient than the inventory they are replacing, and many are incorporating alternative energy to make an even greater impact. Recent popular attention on the cold chain has provided momentum to improve areas where food waste and spoilage occur, and emerging distribution approaches such as e-grocery are reducing the occurrence and impact of food deserts. Even the placement of new facilities has the potential to create extended efficiencies in cold chain transportation. It is incredibly exciting to be a part of a sector that can have such a positive influence.
Trefry and Lyle: It’s fun to ride the wave of popularity surrounding cold storage, and it’s good to see capital markets and developers willing to back a lot of end users who may have struggled in the past getting new facilities built. It’s amazing to see speculative cold evolve from those early ideas into a new market sector. We do worry a bit that the popularity will create a sense of “anyone can do it.” It is easy to make mistakes in designing cold storage facilities, judging market conditions, or during construction, so it’s important to work with a team who has experience and won’t leave you with indoor rain or an expensive building that won’t lease.
Purchase NAIOP’s “Best Practices in Cold Storage Facility Development” e-book, sponsored by Ware Malcomb and FCL Builders, to learn more about cold storage development.