Industrial refrigeration systems are arguably the most critical component of a refrigerated warehouse facility. The industry has evolved significantly over the past decade, and the options are vast when planning a new project or upgrading an existing system.
At NAIOP’s I.CON Cold Storage this week, experts discussed the pros and cons of packaged industrial refrigeration equipment so that investors, developers and operators can make informed decisions. Matthew Hirsch, president, Primus Builders, Inc., spoke along with Michael Jones, AIA, president, Primus Design Services, LLC, and Michael McGinnis, Jr., P.E. president, Innovative Refrigeration Systems, Inc.
“Overall, refrigeration may be one of the single most important decisions that you make as it relates to a refrigerated cold storage distribution center,” said Hirsch.
The capital cost for a refrigeration system could be upwards of 20-30% of the overall initial project capital cost; running the system and its maintenance may account for 60-70% of the overall operating cost of a facility, he said.
The industry continues to expand utilization of prefabricated systems to address cost, schedule, quality and safety. Among the primary benefits to prefabrication, Hirsch said, are reduced overall initial installation cost; accelerated tax depreciation; overall reduction in field labor expenses; and opportunities for scalability. There is also less construction and material waste associated with manufacturing in a controlled environment than infield construction.
“The overall simplification of the design and construction process allows us to accelerate front-end planning as well as the execution piece in the field,” Hirsch said. “You can imagine that ordering refrigeration equipment and starting to prefabricate while the foundations are going in the ground is a huge head start instead of having to wait for the critical pieces to be done before the refrigeration team can mobilize.”
“You’re not having to wait on those items because they’re coming in fully built,” Jones agreed. Inclement weather or difficult conditions at the project site no longer have an impact on the assembly of the equipment; it’s all being done indoors in a controlled environment.
Commissioning and testing are also performed prior to shipping. “The pre-testing is critical, and all done in the factory,” said McGinnis, adding that you can come into the facility and watch your unit being pressure-tested.
The challenges with these prefabricated pieces? They do require enhanced shipping coordination as well as specific job site delivery conditions. Many prefabricated pieces are very large, requiring enhanced safety rigging and access associated to setting larger pieces of equipment.
All panelists agreed that it’s critical for users to understand the options available in the current marketplace and select trusted partners to find the best solution for a project.
“Take time to understand the full spectrum of the cost impact,” said Hirsch, adding that there are opportunities to accelerate projects and take advantage of significant savings with these systems.
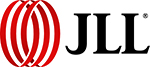
This post is brought to you by JLL, the social media and conference blog sponsor of NAIOP’s I.CON Cold Storage 2023. Learn more about JLL at www.us.jll.com or www.jll.ca.