ABCO Systems started as a pipe and rail provider in New York City’s Garment District over 30 years ago, but as automation and increasing consumer demands have increased the need for more efficient goods distribution, the company has evolved to build and integrate material handling solutions designed for the modern era.
Attendees at I.CON East had the opportunity to tour the company’s facility in Carlstadt, New Jersey, which showcases the latest cutting-edge automation, storage and order fulfillment technologies transforming warehouse and distribution operations. Of the dozens of robotic, artificial intelligence-enabled, cutting-edge tools demonstrated, we’ll highlight a few.
Have you ever received a package with your item thrown inside, surrounded by bubble wrap in an oversized box? The FastFetch IntelliPack® uses AI and computations to select and identify correctly sized packing cartons, tracks replenishment of consumed cartons, and manages carton reordering from a supplier. It cuts shipping costs, reduces packaging labor, reduces landfill waste and reduces fuel consumption required for transporting packages.
“We’ve had companies save a million dollars in their first year just by picking the correct box size,” said Adam Kishpaugh, ABCO’s vice president of solutions development.
The Batch Picking Cart Solution increases the efficiency of distribution center operations by enabling an individual picker to pick multiple orders with one trip through the picking area. Instead of a picker looking down at a tablet or handheld device that tells them to walk to rack 12, bay five, shelf four for their item – often glancing back down at the tablet for reference as they walk the warehouse – the solution allows for a “hands-free, heads-up” mode.
A voice guides the picker through the picking process, lights on product bays highlight each pick location and display pick quantities, then lights on the cart highlight put locations and put quantities. Wireless barcode scanning confirms that the right product was picked.
“When people are picking, 55% of their time is spent traveling the warehouse,” Kishpaugh said. The batch picking cart technology can pick upwards of 250 units per hour vs. the typical 90 units.
Then come the AGVs and AMRs. Addverb’s Zippy 10 sorting robot is an AGV, an autonomous guided vehicle, that follows pre-placed QR codes on a warehouse floor that lay out the robot’s route. These fast-moving robots work well moving products from A to B in unmanned areas without obstacles, emptying trash stations, for example, or other repetitive tasks.
AMRs are autonomous mobile robots, which are self-navigating thanks to sensors and cameras. They work alongside humans easily, navigating around obstacles as needed, with the ability to be reprogrammed to adapt to changing workflows and layouts.
Moving goods from one area of a distribution facility to another is the function of conveyor systems. The concept of conveyance started 150 years ago as coal operators had to determine the most efficient means to move coal out of their mines, Kishpaugh explained.
The systems out there today include belt conveyors (similar to ones used at your local grocery store checkout line), roller conveyors, gravity conveyors and others. Attendees saw a new type of conveyor that looked like a carpet of marbles spaced about a half inch apart. The rolling “marbles” can be programmed to move a package in any direction or angle as needed to divert the item onto the correct conveyor.
Kishpaugh underscored the importance of the speed of diverting or sorting systems by describing current systems as a car stopping at a stop sign, compared to the new technologies that are more like a car exiting a highway via the off ramp. The faster “exit” (sorting/diverting of items) allows more traffic to flow faster.
The sheer number and scale of solutions can be overwhelming, and not every technology is the right fit for every user. By getting to know a company’s throughput, velocities, SKUs, and crunching the data, ABCO works to tailor their solutions accordingly. The company has worked with everyone from mom-and-pop shops to Amazon, Walmart and Tesla.
Then there are the technologies that exist but aren’t even out in the market yet because they remain cost prohibitive. “But it’s just a matter of time until costs come down,” Adam pointed out.
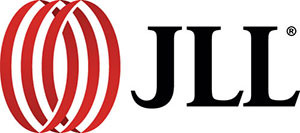
This post is brought to you by JLL, the social media and conference blog sponsor of NAIOP’s I.CON East 2024. Learn more about JLL at www.us.jll.com