By Kathryn Atkins
Roughly 10-12% of the U.S. GDP is tied directly to manufacturing. Moreover, by looking at the tracking of occupier statistics and leasing metrics from all the commercial real estate firms on a quarter-to-quarter average, between 10-15% of leasing activity in the market is tied directly to manufacturing. Bottom line: All industries must consider manufacturing as they explore new ways to diversify their supply chains throughout North America.
In a session at I.CON West this week in Los Angeles, a panel discussed destinations and decision routes tied to the manufacturing landscape. Panelists included Gabriel Padilla Maya, managing director, National Auto Parts Industry Association of Mexico; Enrique Portillo, executive director, Mexico Logistics & Industrial Lead, Cushman & Wakefield; and Jason Tolliver, president, Americas Logistics & Industrial, Cushman & Wakefield.
The size of the manufacturing sector corresponds to the breadth of its problems, agreed the panelists, including:
- The labor shortage in manufacturing is growing. There are currently 440,000 open manufacturing jobs in the U.S.; looking forward, the most conservative estimates of future demand by the National Association of Manufacturing anticipate 3.8 million net new U.S. manufacturing jobs by 2033.
- Energy is in demand. Manufacturers constitute the demand for one-third of all energy consumption needed for data centers, robotics, and other digital inputs to production – not to mention for keeping the lights on.
- Tariffs are the new reality.
One way to help clients broaden their supply chain is by focusing on the concentration of their suppliers in the build-out network in Mexico. Auto parts manufacturing and assembly is a major output from Mexico, and 88% of Mexico’s auto parts production was shipped to the U.S. from January to October 2024. Mexico has taken over the fourth place for auto parts production worldwide after China, the U.S. and Japan.
Challenges for Mexico include impending tariffs, but also their own political and economic roadblocks. Portillo noted that Mexico City has the population to support new manufacturing, yet the city’s rents have seen big growth due to manufacturing plant shortages. In addition, production and development in Mexico City are very complicated, particularly for land purchase, permitting and zoning, which can take at least 18 to 24 months. While attracting investors can be problematic given these disincentives, Japan, Germany, Australia, the U.S. and others continue to invest in CRE in Mexico.
Although the motor of Mexico’s economy is the uncertain automotive sector, panelists agreed that the long-term expectation for manufacturing is bullish.
Every aspect of industrial development must entail numerous key functions, including data-driven site selection, tenant requirements, energy needs, space configuration versus availability, cost of capital, population, and legislation – all within the confines of budgets, risk and return on investment considerations.
Labor availability in numbers remains short, yet the mismatch of labor to the skills required for today’s jobs has created an intractable structural unemployment issue in many countries. The U.S. will need more software, electrical and mechanical engineers educated in the ways of tomorrow’s methods, and not simply on the current approaches. Technology brings innovations faster than people can be trained to use them.
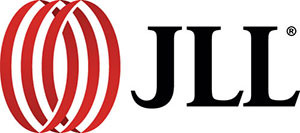
This post is brought to you by JLL, the social media and conference blog sponsor of NAIOP’s I.CON West 2025. Learn more about JLL at www.us.jll.com or www.jll.ca.