Commercial real estate leaders who are looking to reduce the greenhouse gas emissions associated with the construction of new industrial buildings can make use of new measurement tools, data and information, including from the “Embodied Carbon in U.S. Industrial Real Estate Benchmark Survey.” Now that the first article in this series covered the basics of embodied carbon emissions, where they come from, the environmental impact, and the importance of measuring the impact associated with building materials, this piece will focus on steps to achieve a lower embodied carbon footprint.
While the steps to lowering the embodied carbon footprint of a project or portfolio are simple, they are not necessarily easy:
- Establish a baseline by conducting an embodied carbon study.
- Change design standards and material tracking requirements.
- Build differently.
Measuring reduction without fully understanding where you’re starting from is hard. Establishing a baseline allows you to show reduction and celebrate success. If your portfolio stretches across various regions or countries, we recommend selecting a representative project from each region and/or country to review emissions associated with building materials, as it can vary based on the location. For example, colder climates will use more insulation, which increases embodied carbon emissions associated with the project. To avoid the ground getting too hot, warmer climates may choose concrete for paving instead of asphalt, which also increases embodied carbon emissions. Regional differences are essential to understand when setting a baseline.
An industry expert like BranchPattern can help assess your current design standards and specifications and recommend changes requiring lower emissions materials and reducing material quantities. Without realizing it, projects can put more building materials in the project than is necessary, increasing the overall emissions. Engaging the design and construction teams to track material types and quantities and provide submittals is also essential. Some teams may not know how to do this, so training them on what information they need to collect is critical. Ideally, manufacturers are providing product-specific Environmental Product Disclosures (EPDs), or they are participating in an industry-wide EPD study. Also, encourage team communication with material manufacturers to ensure information flows smoothly across all projects.
Finally, we need to build differently. Oftentimes, people are quick to embrace new materials or technologies to reduce emissions associated with building materials. It’s exciting to think of the innovation that will likely occur to help building owners reach their goals. However, there are several steps to achieve before jumping to a low-carbon material substitute.
First, consider reusing a building and/or building materials. Jenny Emrick, global sustainability manager at Prologis, will be one of the panelists during the session “Understanding Carbon Goals and Approaches for Developers” at CRE.Converge in Seattle on Oct. 19. During the panel, Emrick will share a wonderful Prologis success story of how thoughtful consideration of building material reuse saved significant embodied carbon emissions. While ground-up construction can be simpler and easier in many ways, starting with an existing building can represent massive embodied carbon savings – a compelling reason for developers to consider renovating existing building stock before turning to ground-up new construction.
By simply reducing the material quantities in a project, teams can realize huge emissions reduction. Reducing the volume of asphalt pavement, concrete walls and slabs projects not only reduce emissions, but this effort can also save money because the project is using fewer materials. Teams, with the help of sustainability consultants, can also consider optimizing structural framing systems, which reduces the materials needed to achieve the same result.
Designing for disassembly and future reuse is paramount. Being thoughtful about the full life of a building and how the building will be used in 50 years, 100 years or 150 years can be overwhelming, but is extremely important so that we aren’t continuing to emit generations into the future. Consider ways internal wall systems can be reused or other applications for the building structure in the future. Avoiding demolition is critical to saving future emissions.
After considering these first three approaches, we can begin to look at new technologies, systems and materials to help reduce emissions. This really should be the last step when making a conscious effort to reduce emissions, although teams usually revert to it first. There are several opportunities to reduce emissions with low carbon material substitutions:
- Incorporate SCMs (Supplementary Cementitious Materials) in concrete – these materials replace ordinary Portland cement (OPC), which is a major emitter. Traditional SCMs can include fly ash, slag and pozzolan. More innovative SCMs are entering the market as well.
- Incorporate mass timber along with concrete; the beauty of using trees to build is that we can continue to grow the building material, unlike steel or concrete. Also, while the trees grow, they capture carbon. In an industrial building setting, it can be a challenge to completely remove concrete from the project, but by incorporating some timber in the project, you can see reductions in overall emissions.
- TIPS is a wall panel solution with an EPS insulation at the core of reinforced concrete (a sandwich panel, similar to precast walls, but constructed on-site like tilt-up walls). TIPS are structural panels and can reduce the amount of concrete typically required. Using TIPS walls in lieu of traditional tilt-up wall construction could reduce the wall’s carbon emissions by about 20%.
- Nexii panels are a wall system with EPS insulation at the core of reinforced cementitious material. Part of the benefit that Nexii brings is that the system can be taken apart at the end of a building’s life and be reused in a future project. This particular material substitution works best in Industrial projects if the project already has a structural framing system supporting the baseline walls, such as with non-structural precast concrete walls.
- DUCTILCRETE engineered slab systems are typically thinner than traditional concrete slabs and therefore require considerably less Ordinary Portland Cement. Using a DUCTILCRETE could reduce the slab’s carbon emissions by 25% as compared to a baseline slab design.*
- Megaslab significantly reduces Ordinary Portland Cement content and rebar usage, and projects could see the slab’s up to a 39% reduction in embodied carbon emissions by about 40% as compared to a baseline slab design.*
*The estimated reductions are the result of BranchPattern internal assessments, using current data available from manufacturers and proxy EPDs where applicable. Published EPDs would confirm environmental performance.
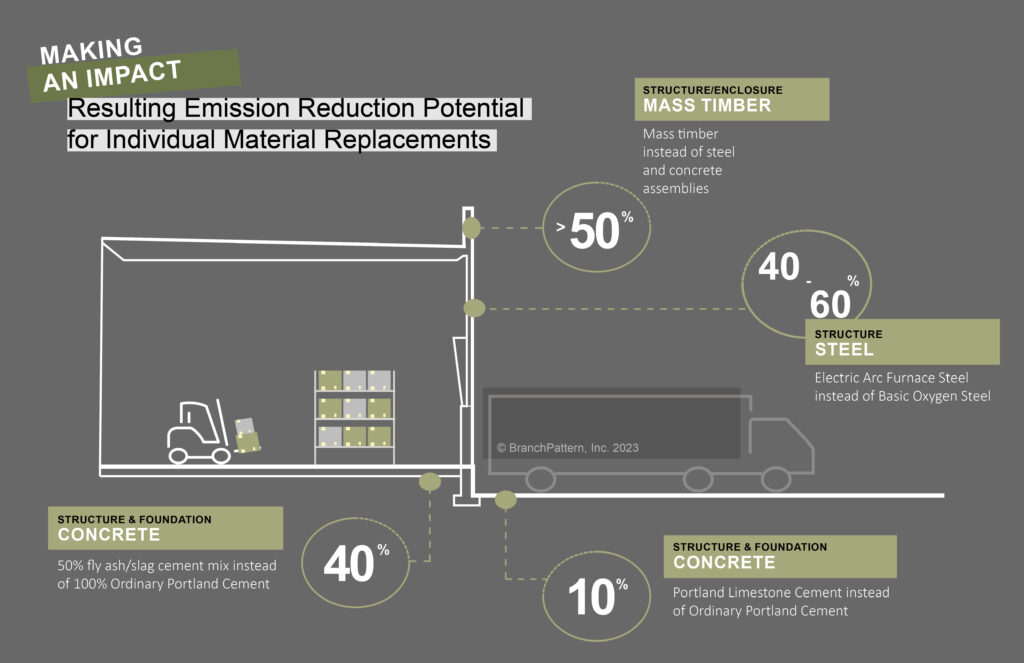
When alternative materials have been exhausted, teams can also select materials with higher recycled content as recycled materials generally have less manufacture process, energy and carbon required than virgin material, for example, consider 100% recycled steel.
Lastly, as the design, material selection and reduction calculations progress, we can begin to consider methods to further diminish emissions through alterations in the construction process. This can be realized through all-electric construction equipment powered by renewable energy. Construction site equipment also accounts for a substantial portion of emissions. Educating general contractors and asking them to track data is a start to build our knowledge of the construction process impact, as well as the emissions associated with transporting building materials to the construction site. Prioritizing the use of locally sourced materials can also demonstrate significant savings.
We hope to see you on Oct. 19 at CRE.Converge as we discuss the case studies mentioned above and the importance of reducing embodied carbon emissions during the construction process.