Mass timber has a bright future within commercial real estate development but there are special hurdles that developers and builders must learn about and overcome, according to commercial real estate experts at NAIOP’s CRE.Converge in Seattle.
Mass timber is an engineered wood product typically made of large panels or beams that are manufactured off-site. The products are engineered to bear weight like steel or concrete but are of lighter weight. Because it is lighter and prefabricated, it can cut down on construction times and also reduce labor costs. The product is also considered more environmentally friendly.
“We’re still in this growth stage where we’re figuring out what products are moving toward standardization, which will make the building system more mainstream,” said mass timber consultant Erica Spiritos, owner, Erica Spiritos LLC, moderator of the panel discussion. Panelists included Robert Gerard, PE, senior discipline engineer, Coffman Engineers of San Diego; Seattle developer and now consultant A-P Hurd, president, SkipStone; and Dean Lewis, director of mass timber and prefabrication, Skanska USA Building, Inc., in Seattle.
“We’re still at a point where we’re tracking every single mass timber project that’s being built, and hopefully at some point we’ll stop tracking because there are so many,” said Spiritos. That said, mass timber has come a long way, she said.
“[Mass timber buildings are] doubling every two years is the research that I’ve seen … in both number of buildings and size of buildings,” Spiritos said. “We’re seeing 500,000-square-foot buildings being constructed with mass timber. And in years past, [for example] in 2017, the largest building that was constructed was 150,000 square feet, so it is coming a long way.”
One notable project is the 8-story, 126-unit Heartwood workforce housing project in Capitol Hill in Seattle. Hurd, who oversaw the design and financing of that project, is now championing the technology.
“It’s a way more sustainable material than concrete, and we knew that it would be a beautiful quality product,” Hurd said. “And Community Roots Housing (the Heartwood owner) is a long-term owner that wants to build beautiful spaces for its residents. So, I think it was a matter of, of course we want to do it, and can we make it work financially? We found that we could.”
Hurd said she expects mass timber to become much more common, even with current challenges in commercial real estate development.
“Every kind of construction is going to have a slowdown here with interest rates where they are, but I don’t see any reason that this wouldn’t continue,” Hurd said. “[The growth] should continue exponentially because every project that happens de-risks all the ones after it.”
However, there are obstacles for the widespread adoption of mass timber, including supply-side issues, local codes and, occasionally, fear of the unknown.
The session began with a poll of the attendees. The first question was, who was working with mass timber? Some 40% said they had projects in design, 33% said they were curious, 17% had projects under construction and 8% “breathe sawdust.”
Next question, what was the biggest concern? It was cost.
And why consider it? Sustainability was the top answer.
Here are some of the highlights of the main discussion areas.
Governments
Motivated to promote sustainability in building, cities, states and the federal government are now getting behind the use of mass timber construction by launching initiatives to fund advancements in the technology and provide grants and incentives to expand its usage. Private companies are also trying to be more sustainable.
Financing
Mass timber is growing in acceptance both by lenders and equity investors. However, there are challenges. There are not as many (if any) comparable buildings made of mass timber in cities. So, developers often must be creative when establishing an appropriate cap rate. For example, Hurd said she compared similar buildings made of concrete and wood-framed structures in Seattle, assuming that a mass timber building would be more valuable and of higher quality than a comparable stick-framed building.
Codes
Local governments, particularly on the West Coast, have become more familiar and comfortable with mass timber construction; however, it is important to involve the local authorities early in the design phase, and involve fire departments in the discussions.
“There are a lot of grey areas that you got to work through with the cities,” Lewis said. “And a lesson learned is just making sure when you’re going through that, the building department may say one thing, but you also have to have the fire department there to sign off on it as well.”
Supply
The availability of mass timber products has improved in the U.S. but still lags Europe’s capacity significantly. Europe’s industry is also standardized. Most of the cross-laminated timber is produced with Spruce pine fir, whereas the product in the U.S. is manufactured with a number of different types of wood, such as Douglas fir, hemlock, spruce and, in the South, yellow pine.
“Our supply chain is way more differentiated than in Europe,” Gerard said. “And so, there are advantages to that because we’re going to have more supply options but it’s also harder to standardize production facilities.”
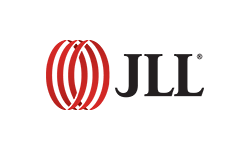
This post is brought to you by JLL, the social media and conference blog sponsor of NAIOP’s CRE.Converge 2023. Learn more about JLL at www.us.jll.com or www.jll.ca.